Custom Plastic Packaging Solutions
Our Capabilities
With 13 CNC milling machines, three in-house prototype thermoformers, and a dedicated team, we turn prototypes around fast – usually within one week. Our in-house capabilities mean our prototypes are very cost-competitive. Because we make them from the same materials and with the same factory process, they are a close representation of your finished product.
Lacerta designs and makes all our production tools in our dedicated, in-house machine shop.
Our factories house 48 state-of-the-art thermoforming machines capable of producing millions of packages per year, and we continuously invest in the latest thermoforming technology to ensure our customers receive low-cost, consistent, high-quality products.
Our tools are designed for custom quick change-overs so that we can respond quickly to evolving customer needs and deliver on a timely basis.
Good for the environment, our five extruders allow us to convert FDA-compliant post-consumer recycled material, respond quickly to changing customer needs, and stay a low-cost supplier.
As a leading supplier of printed lids, our in-house printer can print up to four colors. Our dedicated print department works with customers to develop custom print designs that pop on the shelf.
Lacerta is Safe Quality Food (SQF 8.1 Level II) certified. SQF is recognized by the Global Food Safety Initiative (GFSI) as an approved certification body. Certification means Lacerta has demonstrated a commitment to managing food safety risks and providing safe food products.
Lacerta’s dedicated quality team and quality systems are the cornerstone of our operations. We begin new projects by identifying essential product performance requirements in collaboration with our customers. Throughout the process, our trained operators monitor production through regular quality inspections.
Our materials and parts are consistently evaluated in our Quality Lab, home to the latest measurement tools, such as a Magna-Mike to measure material distribution, an Optical Comparator to evaluate form consistency, and Sealing Tools to measure lidding film compatibility.
Our Process
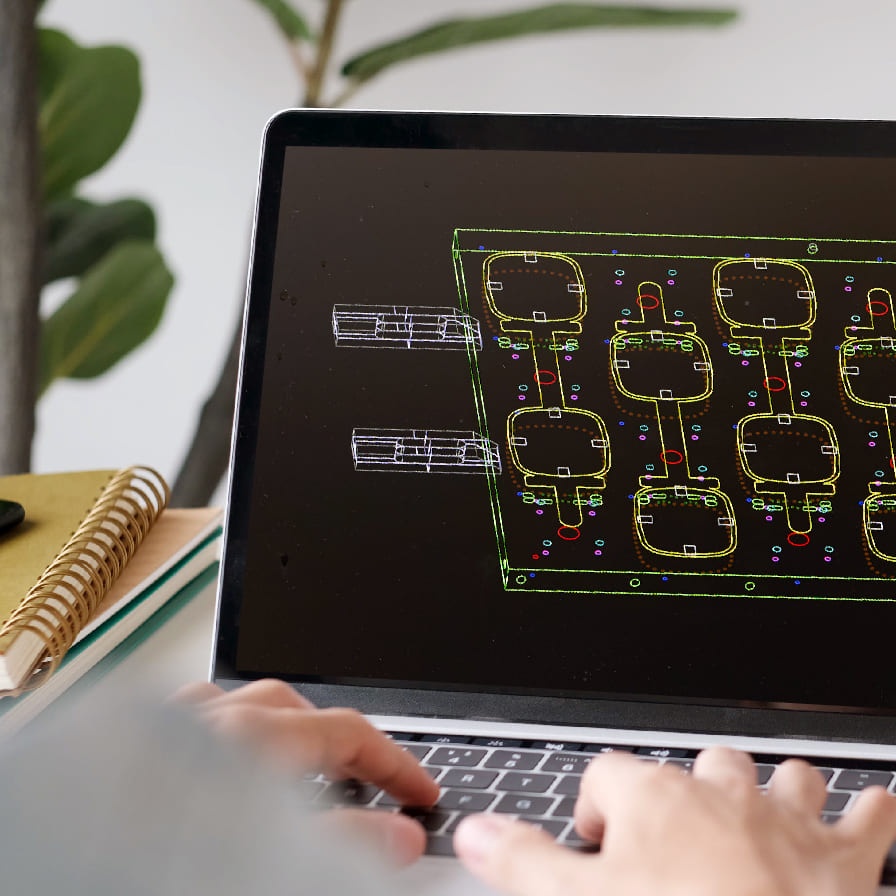
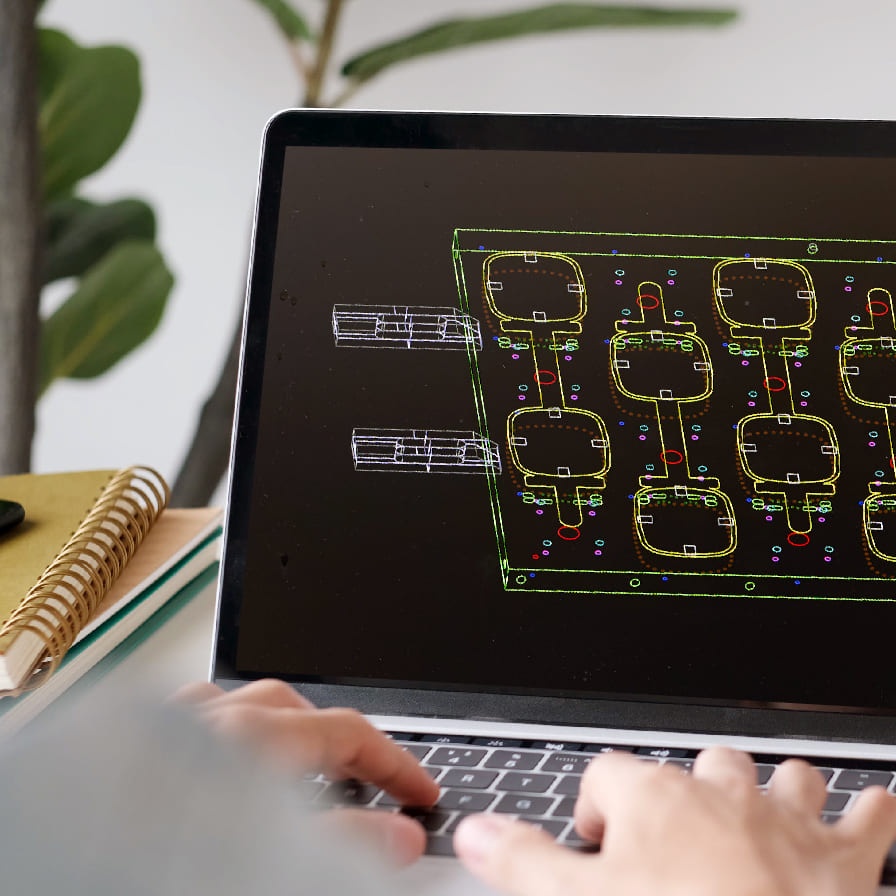
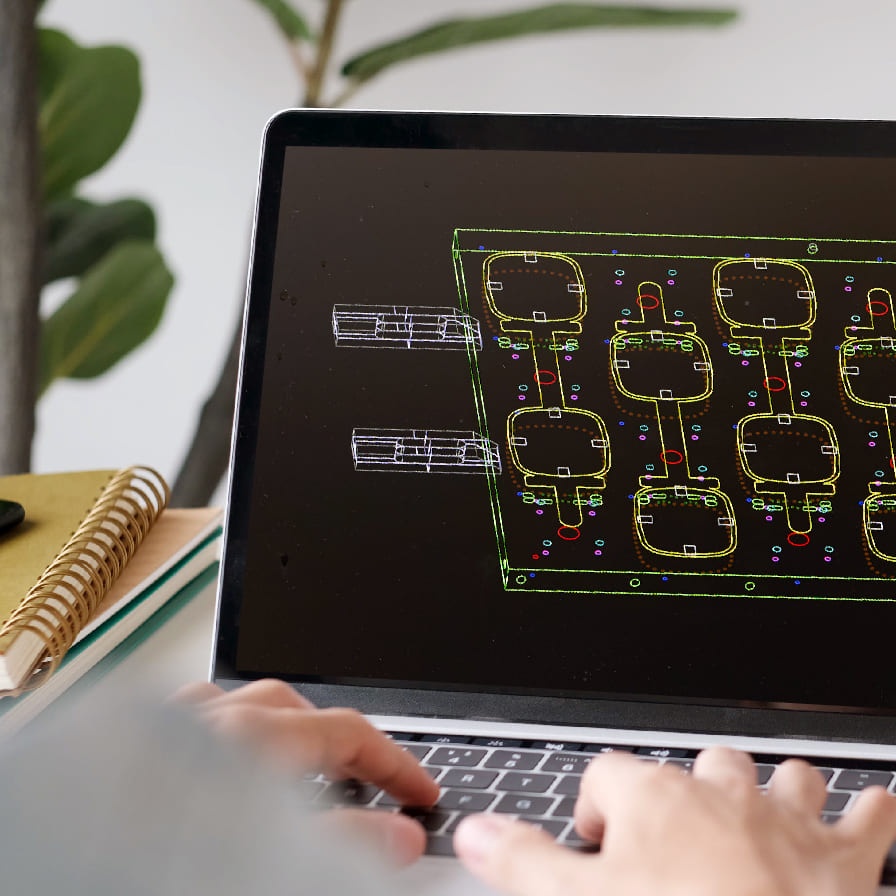
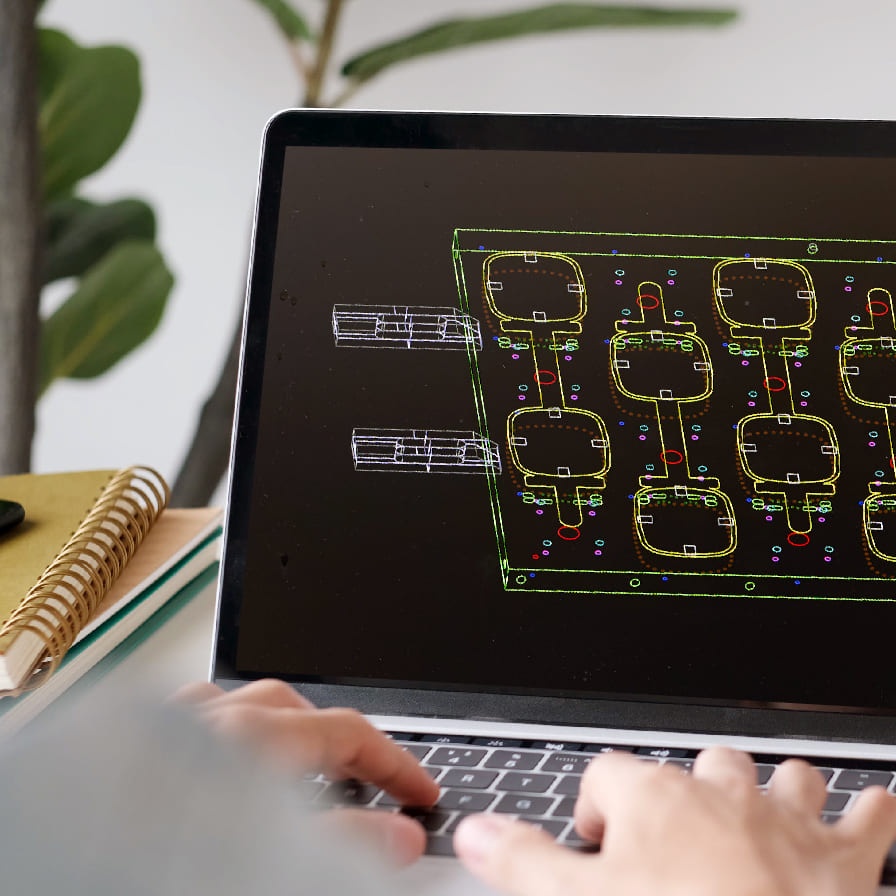
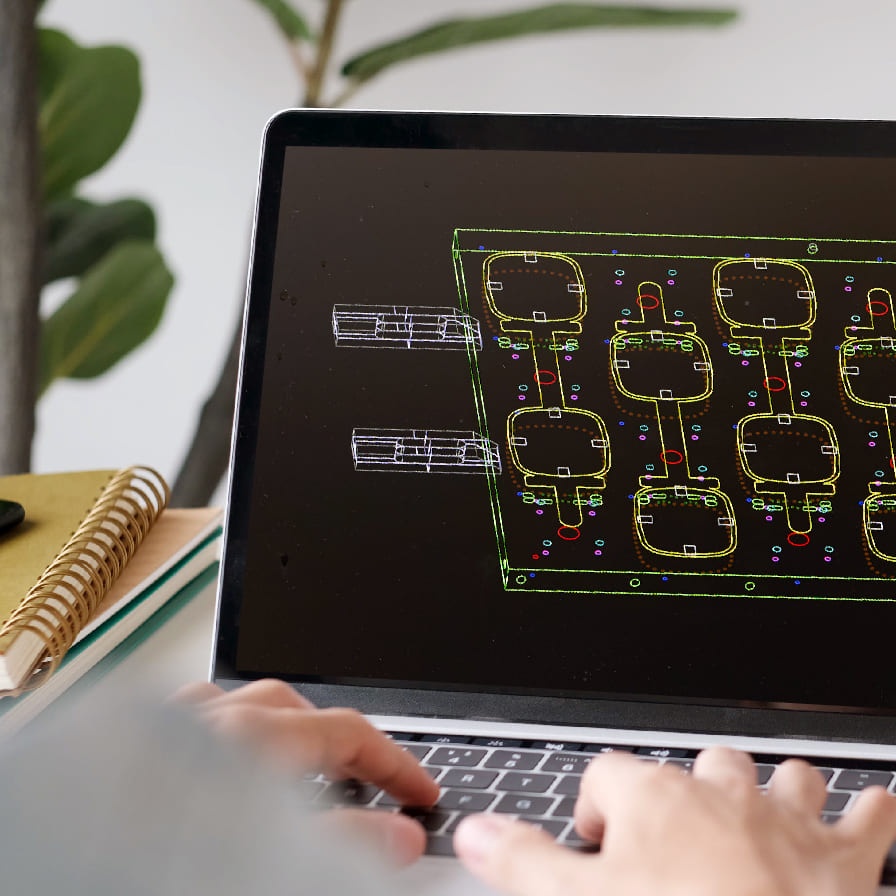
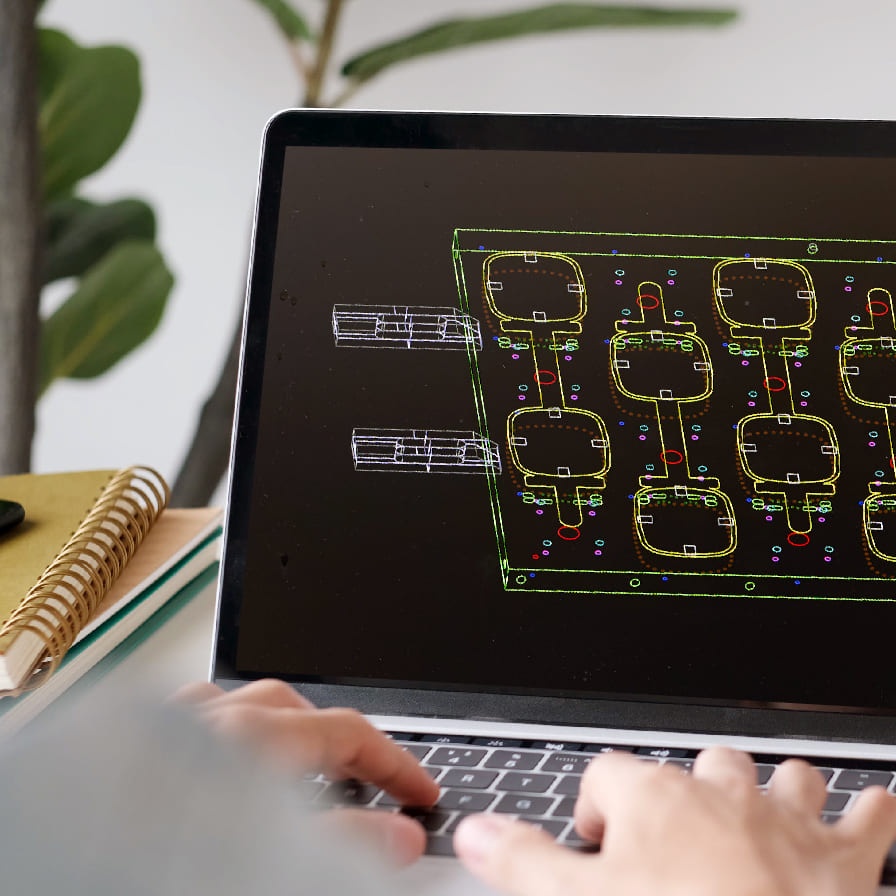
Research & Problem Solving
Creative Design
Concept Visuals
Renderings
In addition to concept drawings, we provide realistic renderings early in the process to showcase the packaging’s appearance.
Considerations
Our customers choose from a broad lineup of packaging options, including Color, Material, Thickness, Barrier, and Coating choices for the ideal result.
Customer Feedback
We give our clients time to review the design, recommend opportunities to iterate, and reach approval.
Prototyping
Our prototyping team provides Ren board or aluminum samples in chosen sustainable material options such as PET, PP, or PCR content.
Features
Depending on the design, we evaluate features such as snap, lid integrity, film seal, and tamper resistance.
Evaluation
We test the material stressors and product-package interaction to make changes necessary for production approval.
Tool Design
Our Engineering and Manufacturing teams collaborate to optimize production efficiency run times. Based on the package, our tools can incorporate robotics and stacking.
Life Cycle Analysis
By creating a Bill of Materials and using the LCA tool, we provide information on the package's sustainability and processes.
Qualification
Then, we evaluate and measure the mold before releasing it for production in one of our cutting-edge thermoforming machines.
Printing
Our customers can print custom graphics, including colors and patterns, on lidding solutions.
Quality and Inspection
Our quality team tests and qualifies samples during both a trial and production run.
Labeling & Shrink Sleeving
Careful label and shrink
sleeve application for a
quality graphic to reflect branding
Release
Finally, we review the qualified items and deliver them to our customers.